Das Unternehmen
proLogistik Schweiz AG

proLogistik Schweiz AG
Seit Juni 2021 gehört XELOG zur proLogistik Gruppe und wurde per 1. April 2024 mit der proLogistik Schweiz AG fusioniert. Bis zum 31. August 2024 ist die proLogistik Schweiz AG noch in Rotkreuz für Sie da. Danach begrüßen wir Sie in der Schaffhauserstrasse 611 in Zürich und wie bisher in Dortmund, Deutschland.
Innerhalb der proLogistik Group bündeln wir die Kompetenzen von mehr als 720 Mitarbeitenden im Bereich Warehouse, Transportation, Hardware und Consulting. Schon heute profitieren viele zufriedene Kunden aus dem Groß- und Einzelhandel von durchgängig optimierten Supply-Chain-Lösungen. Dabei unterstützen wir sowohl Klein- als auch Großunternehmen mit passgenauen Software- sowie Hardwarelösungen bei der digitalen Transformation.
Falls Sie Fragen haben oder Feedback geben möchten, stehen wir Ihnen jederzeit zur Verfügung. Kontaktieren Sie uns über: info-ch@prologistik.com
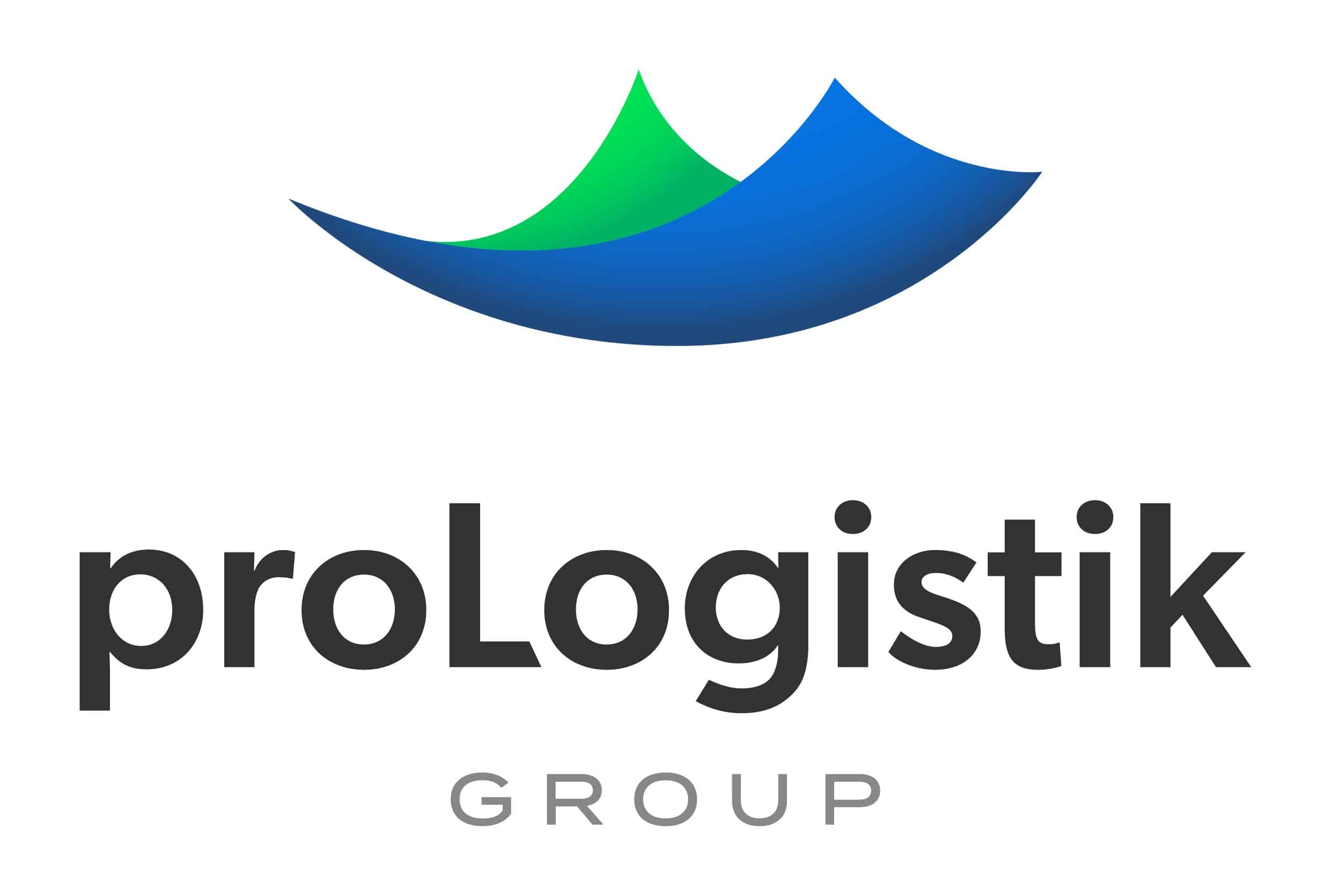
Unsere Kontakte
proLogistik Schweiz AG
(ehemals XELOG AG)
Birkenstrasse 49
CH-6343 Rotkreuz, Schweiz
+41 41 783 8000
info-ch@prologistik.com
proLogistik GmbH
Fallgatter 1
D-44369 Dortmund, Deutschland
+49 231 292 985-00
info@prologistik.com
Support-Nummer
Schweiz: +41 41 783 8001
Deutschland: +49 231 292 985 01
Erfahrungsgemäß gehören viele Fragen nicht in die Kategorie Produkt-Support, sondern betreffen weitere Einsatzmöglichkeiten, Anpassungen von Reports, Erweiterungen des Systems u. v. m. In diesem Falle richten Sie Ihre Frage bitte an Ihren Account-Betreuer oder unser Consulting.
Consulting-Nummer: +41 (0) 41 783 8000
Allgemeine Geschäftsbedingungen der proLogistik Schweiz AG (ehemals XELOG AG)
Die Allgemeinen Geschäftsbedingungen der proLogistik Schweiz AG (ehemals XELOG) bilden einen integrierenden und festen Bestandteil eines jeden Vertrages zwischen Kunde und der proLogistik Schweiz AG (ehemals XELOG).
Hier finden Sie die deutsche Version [Allgemeine Geschäftsbedingungen] und die englische Version [General Tems and Conditions] unserer AGBs.